Corrosion Resistance of DuraBeryllium Plus X-ray Windows Part 2
By Collin Hayward · App and Tech Notes · 25/04/14
X-ray spectroscopy applications and equipment are becoming more portable and are entering harsh environments away from controlled clean environments. This results in a need for more robust X-ray components which are able to handle harsh environments. We are measuring the resistance of different X-ray windows produced by Moxtek Inc. to corrosive and harsh environments.
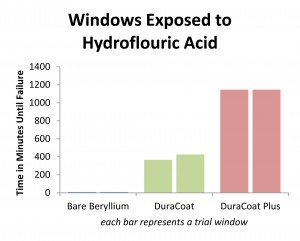
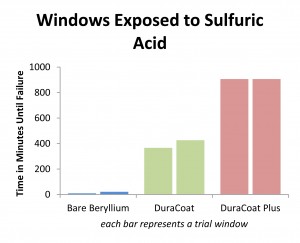
Procedures/ Methods
Three categories of testing were performed to measure the resistance of each type of Moxtek X-ray window to harsh environments: 1. Exposure to high temperatures and then to 1% hydrochloric acid 2. Exposure to a variety of acids at room temperature 3. Exposure to a variety of petroleum based fuels at room temperature Bare uncoated beryllium, DuraBeryllium, and DuraBeryllium Plus windows were used in each test. Each window consisted of a 100 μm thick beryllium foil. The DuraBeryllium had a chemically resistive coating (DuraCoat) applied to the beryllium foil. The DuraBeryllium Plus had two different coatings applied to the beryllium foil (DuraCoat and Plus).High Temperature Bake Followed by 1% HCl Exposure Tests
Most applications require the X-ray windows to be baked at high temperatures in assembling X-ray detectors. The first test was designed to see how chemically resistive the windows were after being baked. Windows were baked at 400°C, 450°C, and 500°C for five hours. One group was baked in air and another in vacuum. After being baked, a solution of 1% hydrochloric acid was dripped on top of the window for a period of time and then checked for leaks on a helium leak detector. A window was considered to have failed if a leak rate greater than 1 x 10-10 mbar*L/s was observed. The windows were repeatedly exposed to acid and checked for leaks until they failed.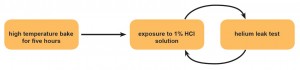
5% Acid Exposure Tests
5% concentrations of hydrochloric acid, sulfuric acid, and hydrofluoric acid were dripped on X-Ray window for a time period followed by a leak check then repeated until found leaky (>1 x 10-10 mbar*L/s).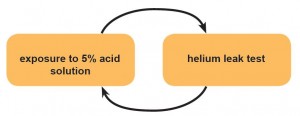
Petroleum Based Fuels Test
The final test consisted of exposing the X-ray windows to a variety of common petroleum based fuels. Windows were dipped into regular unleaded gasoline, diesel fuel, and kerosene for month long intervals and then checked for leaks on a helium leak detector.Experimental Results
High Temperature Bake Followed by 1% HCl Exposure Results
The following two graphs show the results of the X-ray windows exposed to high temperatures and to 1% hydrochloric acid.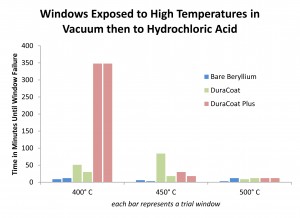

5% Acid Exposure Results
The graphs below show the results of the windows exposed to 5% concentrations of hydrochloric acid, sulfuric acid, and hydrofluoric acid.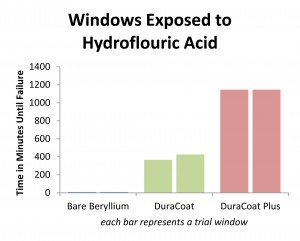
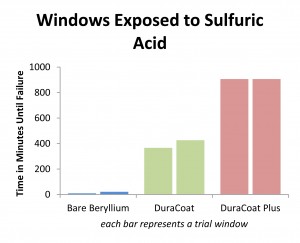
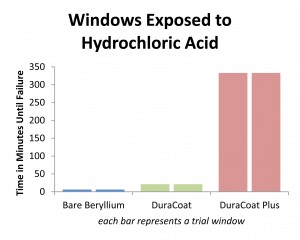